Carbon Steel:
The Backbone of Strength
- Alloyours
carbon steel products
Carbon Steel: Forging Excellence, Alloying Possibilities!
low carbon steel
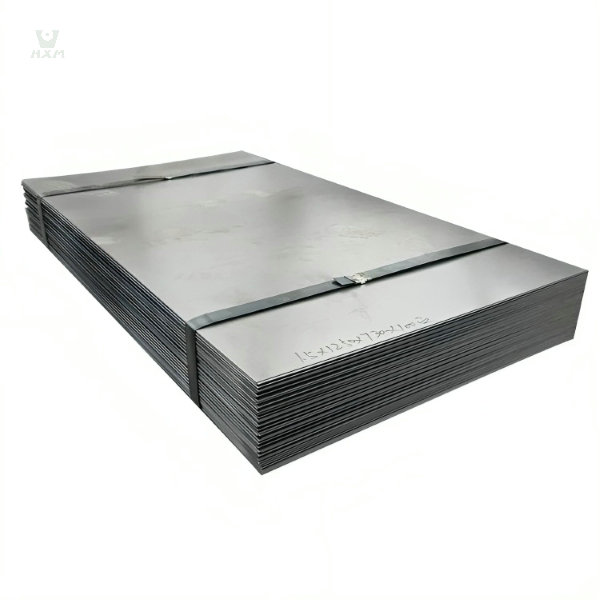
middle carbon steel
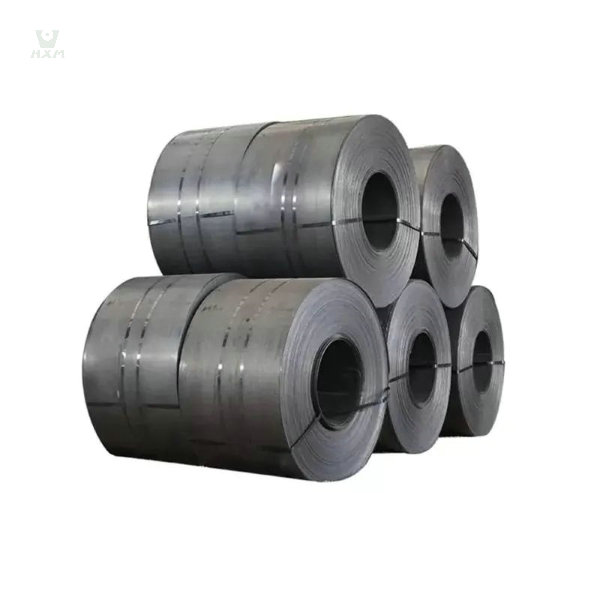
high carbon steel
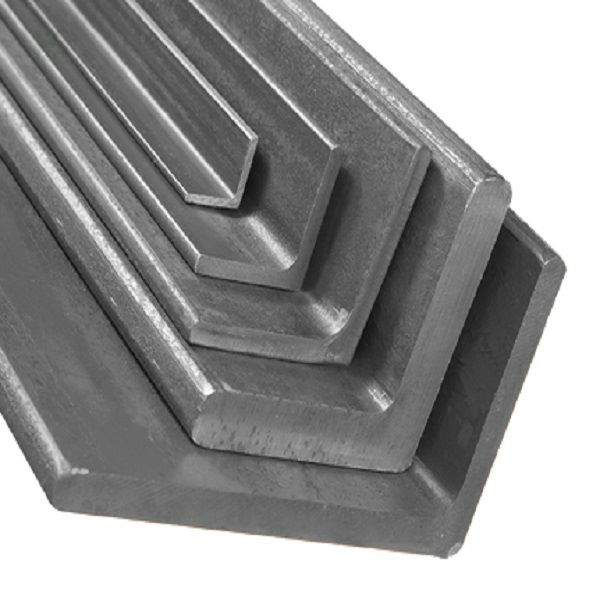
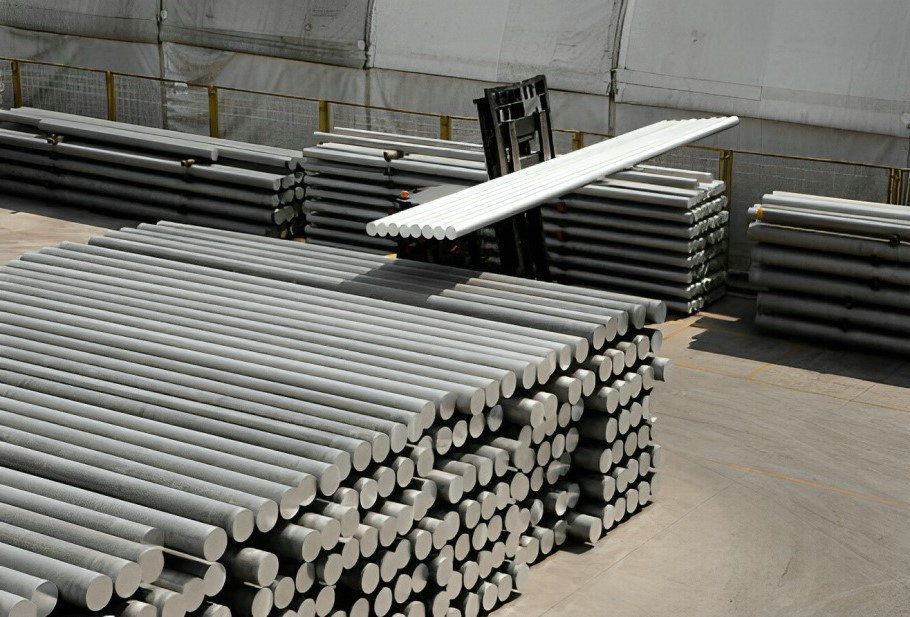
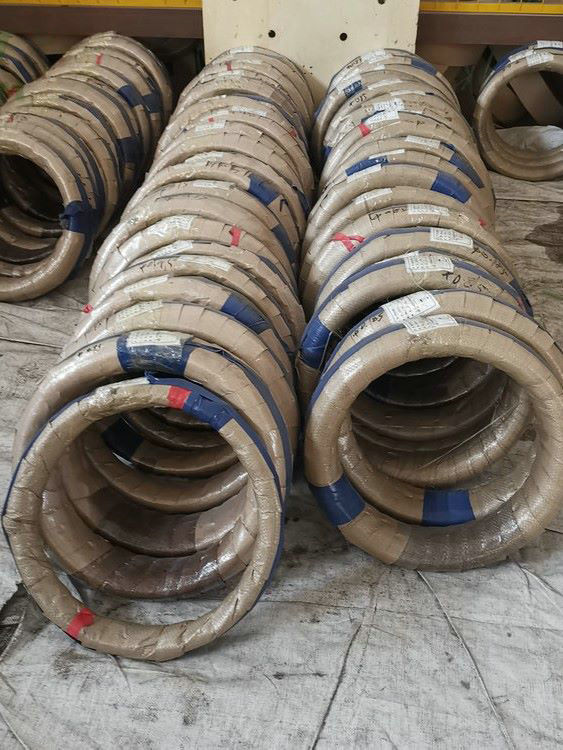
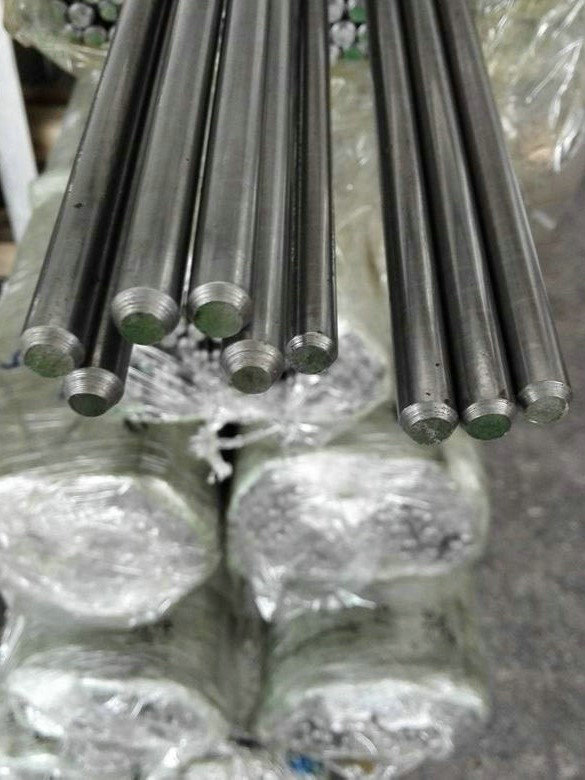
Ready To Provide Your Best Carbon Steel Products
Alloyours: Your Trusted Partner for High-Quality Alloys and Custom Solutions.
Years of Expertise
Peoples Served
Engaged Partners
Tons Exported
We Provide The Best Service
Our services encompass a wide range of alloys, providing tailored solutions to meet your unique industrial needs.
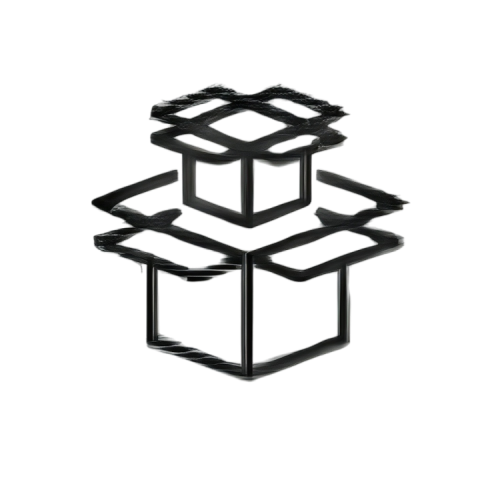
High-Quality Alloy Supply

Custom Global Alloy Solutions
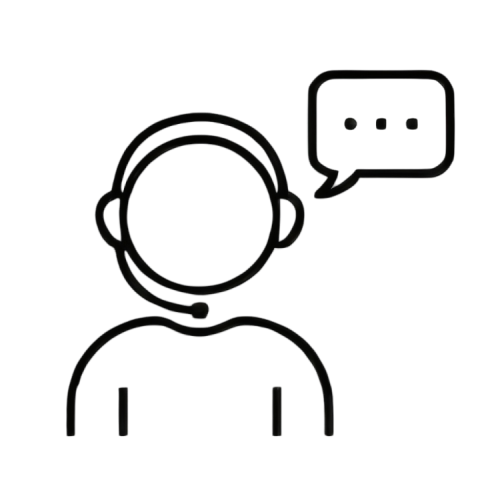
Expert Technical Support

Timely Delivery Assurance
What is carbon steel?
Carbon steel is a versatile and widely used category of steel alloy distinguished primarily by its high carbon content, typically ranging from 0.05% to 2.1%. This elevated carbon concentration differentiates it from other steel types, such as stainless steel or alloy steel, which have lower carbon percentages.
Carbon steel derives its name from the significant presence of carbon, a key alloying element that profoundly influences its properties. Here are the essential characteristics and uses of carbon steel:
Strength and Durability: Carbon steel exhibits excellent strength and durability due to its higher carbon content. It is known for its capacity to withstand mechanical stress and is frequently employed in structural applications, including buildings, bridges, and infrastructure.
Versatility: Carbon steel is incredibly versatile, with various grades tailored to specific applications. Low-carbon steel is malleable and well-suited for tasks requiring shaping and welding, while high-carbon steel offers exceptional hardness and wear resistance, making it suitable for cutting tools and machinery components.
Machinability: Many carbon steel grades are easily machined, allowing for precision shaping and manufacturing. This makes it a preferred material in the production of automotive parts, pipes, and fittings.
Cost-Effective: Carbon steel is often more cost-effective than other alloyed steels, making it a preferred choice for a wide range of applications where the enhanced properties of alloyed steels are not necessary.
Weldability: While weldability can be affected by the carbon content, modern welding techniques and appropriate filler materials have made carbon steel weldable. It is essential to choose the right grade of carbon steel and welding processes to ensure proper weld quality.
Carbon steel suppliers play a vital role in the industry by providing a diverse range of carbon steel materials, each tailored to specific industrial needs. These suppliers ensure a consistent supply of high-quality carbon steel products for applications ranging from construction and manufacturing to infrastructure development.
How is carbon steel classified?
Carbon steel can be categorized based on its carbon content, alloying elements, and performance characteristics. Here are some common ways to categorize carbon steel:
Based on carbon content
- Mild Steel: Carbon content is usually less than 0.30%, with good ductility and weldability. Widely used in the manufacture of thin plates, pipes and general structural components.
- Medium Carbon Steels: Containing between 0.30% and 0.60% carbon, they have high strength. Commonly used in the manufacture of gears, shafts and automobile parts.
- High Carbon Steels: Usually contain more than 0.60% carbon and have very high hardness and wear resistance. Suitable for tools, springs and bearings.
Based on alloying elements
- Unalloyed Carbon Steel: Consists of iron and carbon with no other alloying elements.
- Low Alloy Carbon Steels: Contain small amounts of alloying elements such as manganese, chromium, molybdenum, etc. to improve specific properties such as strength and corrosion resistance.
- High Alloy Carbon Steels: Contain large amounts of alloying elements and are typically used for specialized applications with high temperature and corrosion resistance requirements.
Based on application and properties
- Structural Carbon Steels: Used in building construction and are known for their strength and ductility.
- Mechanical Carbon Steels: Used in the manufacture of mechanical parts, bearings and gears, characterized by high strength and wear resistance.
- Free Cutting Steels: Containing special elements to improve machinability, suitable for bolts, nuts and free cutting parts.
Based on the production process
- Hot Rolled Carbon Steels: Manufactured through the hot rolling process and are commonly used in structural and fabrication applications.
- Cold Rolled Carbon Steel: Produced through the cold rolling process, it has a smooth surface and is suitable for applications that require high surface quality.
Carbon steel suppliers play a pivotal role in providing a wide range of carbon steel materials, ensuring that customers receive a quality product that meets their specific industrial needs.
carbon steel VS. stainless steel
These two materials are fundamental in the world of metallurgy, each with its unique set of properties and applications.
Carbon Steel: Primarily consists of iron and carbon, with carbon content ranging from 0.05% to 2.1%. It may contain small amounts of other alloying elements.
Stainless Steel: Contains iron, chromium, and varying amounts of nickel, molybdenum, or other alloying elements, with a minimum of 10.5% chromium to resist corrosion.
Carbon Steel: Prone to corrosion when exposed to moisture and aggressive environments. Requires protective coatings or treatments to prevent rust.
Stainless Steel: Highly resistant to corrosion and staining due to the presence of chromium, making it suitable for applications where corrosion is a concern.
Carbon Steel: Offers good strength and durability, depending on carbon content. Higher carbon levels result in increased hardness and strength.
Stainless Steel: Generally has lower strength compared to high-carbon steel but maintains excellent corrosion resistance.
Carbon Steel: Typically magnetic unless it has been significantly alloyed or heat-treated.
Stainless Steel: Can be either magnetic or non-magnetic, depending on its composition and processing.
Carbon Steel: Widely used in construction, automotive, manufacturing, and structural applications where strength and cost-effectiveness are essential. Common in tools and machinery.
Stainless Steel: Preferred in environments where corrosion resistance is crucial, such as the food industry, medical devices, aerospace, and marine applications.
Carbon steel suppliers provide a range of carbon steel materials, while stainless steel suppliers specialize in stainless steel alloys. Understanding these differences is vital when selecting the right material for specific applications, considering factors such as corrosion resistance, strength, and cost-effectiveness.
carbon steel VS. regular steel
The world of steel is diverse, comprising a wide array of alloys, each designed to meet specific needs. A fundamental distinction within this realm is between carbon steel and what is often referred to as “regular” steel. While both share a common foundation of iron, they diverge significantly in terms of composition, characteristics, and applications. In this comparison, we delve into the core differences between these two steel types, shedding light on when and why one might be preferred over the other in various industrial and everyday contexts. Understanding this contrast is essential for informed material choices and optimal performance in countless applications.
Carbon Steel: Carbon steel is a type of steel primarily composed of iron and carbon, with carbon content typically ranging from 0.05% to 2.1%. It may also contain small amounts of other alloying elements.
Regular Steel: In the context of carbon steel, the term “regular steel” is often used interchangeably, as carbon steel is the most common and widely used form of steel.
Carbon Steel: The defining characteristic of carbon steel is its relatively high carbon content, which sets it apart from other steel types.
Regular Steel: When people refer to “regular steel,” they are often referring to carbon steel, emphasizing its ubiquity in various applications.
Carbon Steel: Offers good strength and durability, depending on carbon content. Higher carbon levels result in increased hardness and strength.
Stainless Steel: Generally has lower strength compared to high-carbon steel but maintains excellent corrosion resistance.
Carbon Steel: Typically magnetic unless it has been significantly alloyed or heat-treated.
Stainless Steel: Can be either magnetic or non-magnetic, depending on its composition and processing.
Carbon Steel: Widely used in construction, automotive, manufacturing, and structural applications where strength and cost-effectiveness are essential. Common in tools and machinery.
Stainless Steel: Preferred in environments where corrosion resistance is crucial, such as the food industry, medical devices, aerospace, and marine applications.
Carbon steel suppliers provide a range of carbon steel materials, while stainless steel suppliers specialize in stainless steel alloys. Understanding these differences is vital when selecting the right material for specific applications, considering factors such as corrosion resistance, strength, and cost-effectiveness.
Manufacturing Process of Carbon Steel
Carbon steel, a widely used material in various industries, undergoes a well-defined manufacturing process to achieve its diverse range of properties. Here’s a detailed breakdown of the production journey, where carbon steel suppliers play a pivotal role:
Ironmaking
In the ironmaking stage, this raw ore is subjected to a high-temperature blast furnace. Inside the furnace, it encounters a mixture of coke (a form of carbon), limestone, and iron ore. This intense heat triggers a chemical reaction, yielding molten iron as the primary product. This molten iron, known as "hot metal," is the initial step in the carbon steel production chain.
Steelmaking
To transform hot metal into carbon steel, it goes through a refining process known as steelmaking. Two primary methods are employed: Basic Oxygen Furnace (BOF): In this method, oxygen is injected into the hot metal, oxidizing impurities like carbon, silicon, and manganese. The result is a purer form of iron, known as liquid steel. Electric Arc Furnace (EAF): Alternatively, an Electric Arc Furnace melts scrap steel and refines it using an electric current, creating liquid steel.
Casting
The liquid steel, whether from BOF or EAF, is then cast into various forms. It can be poured into molds to produce ingots, or in a continuous casting process, it's transformed into slabs, blooms, or billets, depending on the desired end product.
Forming
The next phase involves shaping the steel to its final specifications. This can be achieved through either hot-rolling or cold-rolling processes, depending on the intended product. Hot-rolling involves heating the steel and passing it through rollers, while cold-rolling is performed at room temperature. These processes result in sheets, plates, bars, and rods, among other forms.
Finishing
To enhance the properties and characteristics of carbon steel, various finishing operations are conducted. These may include: Annealing: The steel is heated and then slowly cooled to relieve internal stresses and improve its ductility. Tempering: This heat treatment process fine-tunes the hardness and toughness of the steel, optimizing it for specific applications. Coating: In some cases, carbon steel is coated with materials like zinc to enhance corrosion resistance.
Throughout this intricate manufacturing process, carbon steel suppliers play a central role in sourcing, processing, and delivering carbon steel products tailored to the unique needs of industries worldwide. They ensure that high-quality carbon steel materials are readily available for construction, manufacturing, and various industrial applications.
Building The Future
Latest From the Blog
contact us
Let's Get in
Touch
Email Address
market004@alloyours.com
Call Us
+86 13052085117
Address
Minhang District, Shanghai, China