Alloyours
Forging the Future with Iron Alloys:
Unyielding Strength, Infinite Possibilities.
Stainless steel products
carbon steel products
low carbon steel
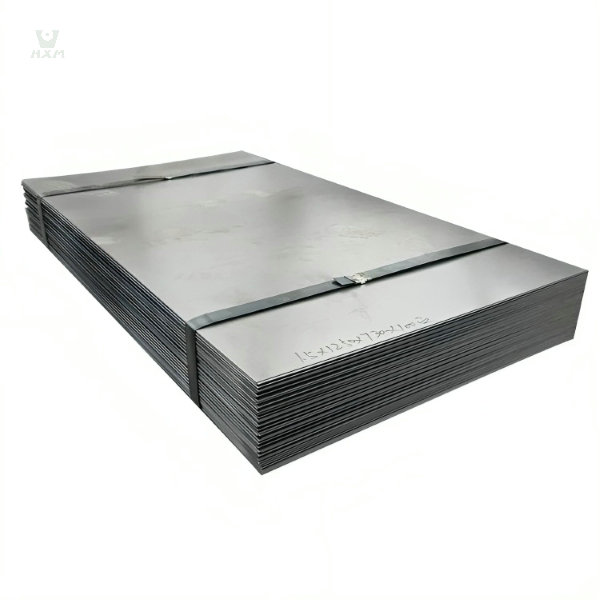
middle carbon steel
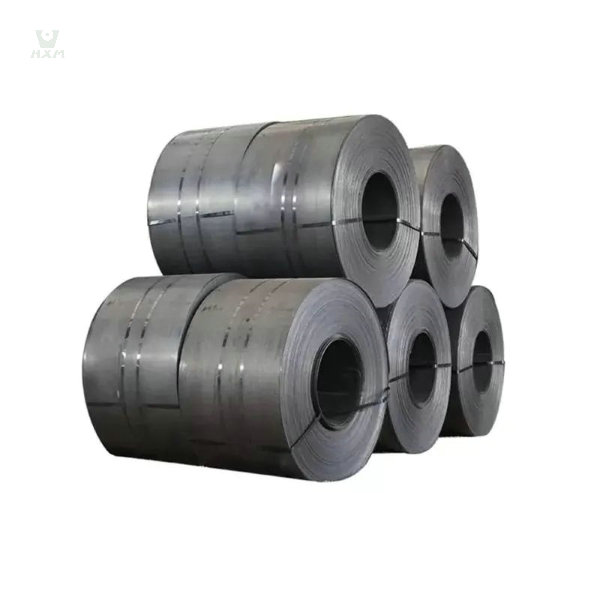
high carbon steel
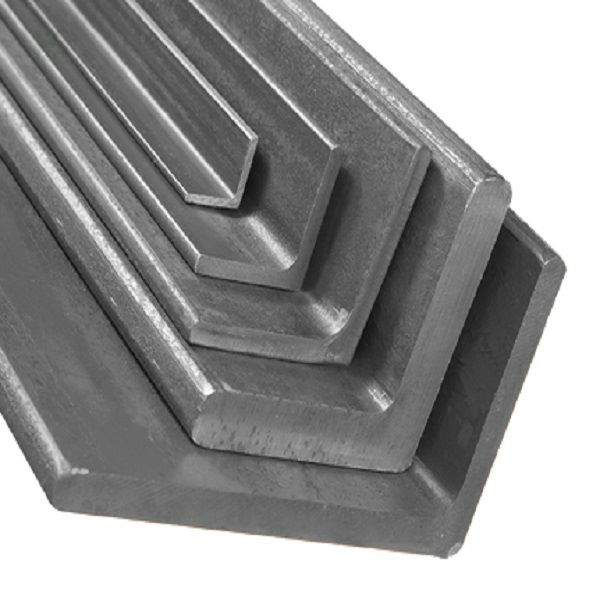
Introduction to Iron Alloys
Iron alloy refers to a metallic substance composed primarily of iron, along with the intentional addition of other elements, known as alloying elements. The purpose of incorporating these alloying elements is to modify the properties and characteristics of iron, resulting in a material with enhanced performance for specific applications.
Iron, as an elemental metal, possesses certain inherent properties such as malleability, ductility, and a relatively low tensile strength. However, pure iron lacks some essential attributes required for diverse industrial applications, such as increased strength, improved corrosion resistance, and enhanced hardness.
To overcome these limitations, iron is combined with alloying elements such as carbon, manganese, nickel, chromium, and others. These elements interact with the iron matrix at the atomic level, influencing the material’s microstructure and resulting in notable changes in its mechanical, physical, and chemical properties.
The precise composition and concentration of alloying elements play a crucial role in determining the specific characteristics of the iron alloy. For example, the addition of carbon in different proportions leads to the formation of carbon steels or cast irons, each with distinct properties and applications.
Iron alloys find extensive applications in industries such as construction, automotive manufacturing, aerospace, electrical engineering, machinery production, and more. These alloys offer advantages such as increased strength, improved hardness, better heat resistance, enhanced corrosion resistance, and tailored magnetic properties.
By incorporating alloying elements into iron, manufacturers can create alloys with desired properties that meet the diverse needs of their customers. Alloy suppliers play a vital role in providing these specialized iron alloys to industries worldwide, ensuring a reliable and efficient supply of materials for various applications.
Classification of Iron Alloys
Iron alloys can be classified based on the types and concentrations of alloying elements added to iron. These alloying elements alter the microstructure and properties of iron, resulting in different categories of iron alloys. Here are the primary classifications of iron alloys:
Iron alloys can be classified into several categories based on their composition and properties. The primary classifications of iron alloys include:
Carbon Steels: Carbon steels are iron alloys that primarily consist of iron and carbon, with carbon content, typically ranging from 0.02% to 2.1% by weight. The amount of carbon determines the hardness, strength, and other mechanical properties of the steel. Carbon steels are widely used in the construction, automotive, and machinery industries.
Alloy Steels: Alloy steels are iron alloys that contain additional alloying elements apart from carbon. These alloying elements can include elements like manganese, chromium, nickel, molybdenum, and vanadium. Alloy steels exhibit improved properties such as increased strength, hardness, and wear resistance compared to carbon steels. They find applications in diverse industries, including aerospace, automotive, and manufacturing.
Stainless Steels: Stainless steels are iron alloys that contain a minimum of 10.5% chromium along with other alloying elements like nickel and molybdenum. The addition of chromium provides stainless steel with excellent corrosion resistance. Stainless steels are widely used in applications where resistance to rust and corrosion is essential, such as in the food industry, architecture, and medical equipment.
Tool Steels: Tool steels are specialized iron alloys designed for applications that require high hardness, toughness, and wear resistance. These alloys often contain elements like tungsten, molybdenum, vanadium, and cobalt. Tool steels are commonly used in the production of cutting tools, molds, and dies.
Cast Iron: Cast iron is an iron alloy that contains a high carbon content (above 2%) and often includes additional alloying elements such as silicon. Cast iron exhibits excellent castability, high wear resistance, and good heat retention. It finds applications in engine blocks, pipes, cookware, and architectural elements.
Maraging Steels: Maraging steels are iron alloys known for their exceptional strength and toughness. These steels undergo a unique heat treatment process called maraging, which involves aging at elevated temperatures to achieve their desired properties. Maraging steels are commonly used in aerospace, defense, and tooling applications.
Each category of iron alloy offers distinct properties and advantages, making them suitable for various industrial applications. Iron alloy suppliers specialize in providing these different types of iron alloys to meet the specific needs and requirements of different industries.
Specifications to consider
When selecting metal alloys, it is crucial to analyze the desired dimensions and specifications for the intended application. The following dimensions should be taken into consideration:
- Outer Diameter (OD)
- Inner Diameter (ID)
- Overall Length
- Overall Thickness
In addition to dimensions, there are various specifications that hold significance based on the intended application. These specifications include:
The shape of the metal alloy component or structure is an important consideration as it can affect its functionality, ease of manufacturing, and integration into the overall system.
Tensile strength is the maximum stress a metal alloy can withstand without fracturing when subjected to tension. It is an essential property to evaluate the material’s ability to resist pulling forces.
Yield strength refers to the stress at which a metal alloy begins to exhibit permanent deformation or yield. It is an important parameter to assess the material’s ability to withstand applied loads without permanent deformation.
The melting point indicates the temperature at which the metal alloy changes from a solid to a liquid state. It is crucial to know the melting point to determine the alloy’s suitability for specific manufacturing processes and applications.
Conductivity measures the ability of a metal alloy to conduct electricity or heat. Depending on the application, high or low conductivity may be desired.
Corrosion resistance indicates the metal alloy’s ability to withstand degradation caused by environmental factors, such as moisture, chemicals, or exposure to harsh conditions.
Ductility refers to the material’s ability to deform under tensile stress without fracturing, while malleability refers to its ability to be easily shaped or formed. These properties are important in applications where bending, forming, or shaping is required.
Collaborating with reputable iron alloy suppliers ensures access to high-quality materials, technical support, and a wide range of options. Whether it’s for construction, automotive, machinery, or other industries, iron alloy suppliers play a crucial role in meeting the demands of customers seeking reliable and top-notch iron alloy materials.
Production Process of Iron Alloys
The production of iron alloys involves several steps that transform raw materials into the desired alloy compositions. The typical production process for iron alloys is as follows:
Raw Material Preparation: The production process begins with the collection and preparation of raw materials. Iron alloys are primarily composed of iron, along with various alloying elements. These alloying elements can include carbon, manganese, chromium, nickel, molybdenum, and others. The raw materials are carefully selected and processed to ensure the desired chemical composition.
Melting: The prepared raw materials are then melted in a furnace. The furnace is designed to withstand high temperatures and is capable of reaching the melting point of iron and the alloying elements. The materials are heated until they reach a molten state, allowing for the proper mixing and formation of the alloy.
Alloying: Once the raw materials are melted, alloying elements are added to achieve the desired composition. The specific alloying elements and their quantities depend on the desired properties and characteristics of the iron alloy. The alloying elements are carefully measured and added to the molten iron, ensuring a uniform distribution.
Degassing and Refining: To remove impurities and gases from the molten metal, a degassing and refining process is carried out. This involves the use of various techniques such as vacuum degassing or the addition of refining agents to enhance the purity and quality of the alloy.
Casting: After the alloy is properly refined and degassed, it is ready for casting. The molten alloy is poured into molds or castings of desired shapes and sizes. Different casting methods can be employed, including sand casting, investment casting, or continuous casting, depending on the specific requirements of the alloy and the intended application.
Solidification and Cooling: Once the alloy is poured into the molds, it undergoes a solidification process. The molten metal cools and solidifies, taking the shape of the mold cavity. This step is critical for achieving the desired microstructure and properties of the alloy.
Heat Treatment: Depending on the alloy composition and desired properties, heat treatment processes such as annealing, quenching, and tempering may be employed. These processes help to optimize the mechanical properties, hardness, and toughness of the alloy.
Finishing and Quality Control: After the casting and heat treatment processes, the iron alloy undergoes finishing operations such as machining, grinding, polishing, and surface treatment to achieve the desired final product specifications. Quality control measures are implemented throughout the production process to ensure that the alloy meets the required standards and specifications.
Final Inspection and Packaging: Once the production process is complete, the iron alloy undergoes a final inspection to verify its quality, dimensional accuracy, and overall compliance with customer requirements. The alloys are then appropriately packaged for storage, transportation, and delivery to customers.
The production process of iron alloys is a complex and precise undertaking that requires expertise, careful monitoring, and adherence to industry standards. By following these steps, iron alloy suppliers can produce iron alloys with the desired composition, properties, and quality for a wide range of applications in various industries.
Versatile Applications of Iron Alloys
Iron alloys, renowned for their strength and durability, find wide-ranging applications in machinery, transportation vehicles, and structural engineering. Their robust properties make them ideal for diverse applications, including:
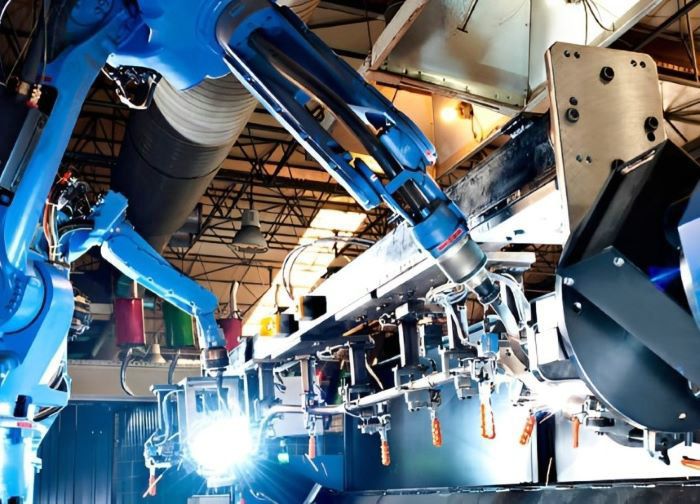
Machinery and Tools
Iron alloys, such as cast iron and various grades of steel, are extensively employed in the manufacturing of machinery and tools. These alloys provide exceptional strength, wear resistance, and heat tolerance, making them suitable for components like gears, shafts, bearings, and cutting tools. Their reliability and longevity contribute to the efficiency and productivity of machinery across industries.
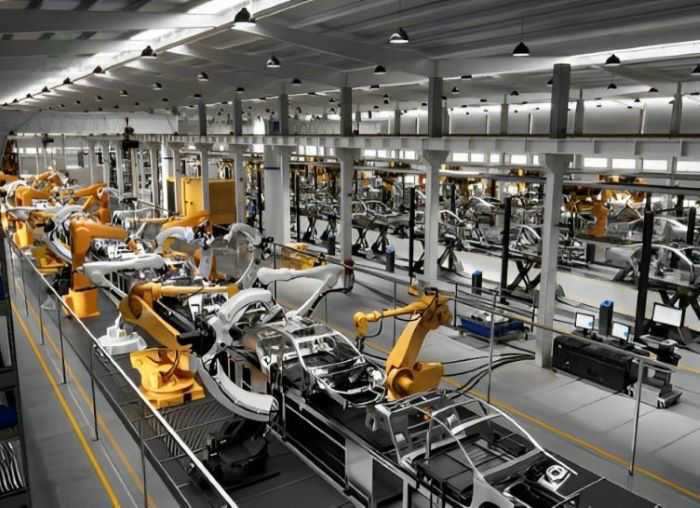
Vehicles
Iron alloys play a pivotal role in the automotive and transportation sectors. They are used in the production of engine blocks, cylinder heads, crankshafts, and other vital components. Additionally, iron-based alloys, like ductile iron, are employed for applications that require high strength, impact resistance, and dimensional stability. The use of iron alloys ensures the structural integrity and longevity of vehicles, including cars, trucks, and motorcycles.
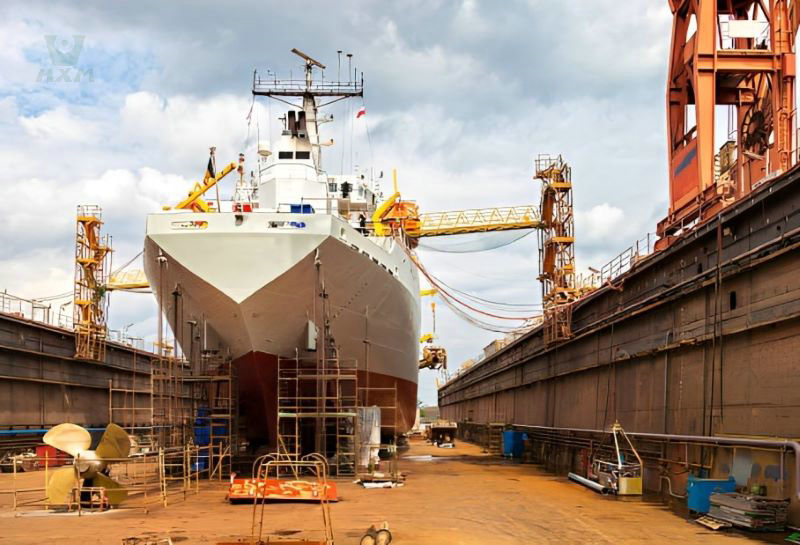
Ship Hulls
Iron alloys, particularly high-strength steels, are essential in the construction of ship hulls. These alloys offer excellent strength-to-weight ratios and corrosion resistance, enabling the construction of robust and seaworthy vessels. The use of iron alloys ensures the structural integrity and reliability of ships, enhancing their performance and safety in challenging marine environments.

Structural Elements
Iron alloys serve as key materials for the construction of various structural elements in buildings, bridges, and aircraft. Structural steel, an iron alloy with specific composition and properties, is widely utilized in the construction industry. It provides strength, ductility, and versatility, enabling the creation of sturdy and resilient structures. Iron alloys contribute to the stability, load-bearing capacity, and overall safety of buildings, bridges, and aircraft.
The versatile applications of iron alloys in machinery, transportation, and structural engineering highlight their significance in modern industries. By harnessing the strength and durability of iron alloys, iron alloy suppliers and engineers can ensure the reliability, performance, and longevity of machinery, vehicles, ships, and critical structural elements. The continuous development and utilization of iron alloys drive technological advancements, infrastructure growth, and global connectivity.
Why Choose Alloyours

Your Trusted Iron Alloy Suppliers
At Alloyours, we stand out as your trusted iron alloy suppliers, offering a wide range of benefits and advantages that set us apart from the competition.
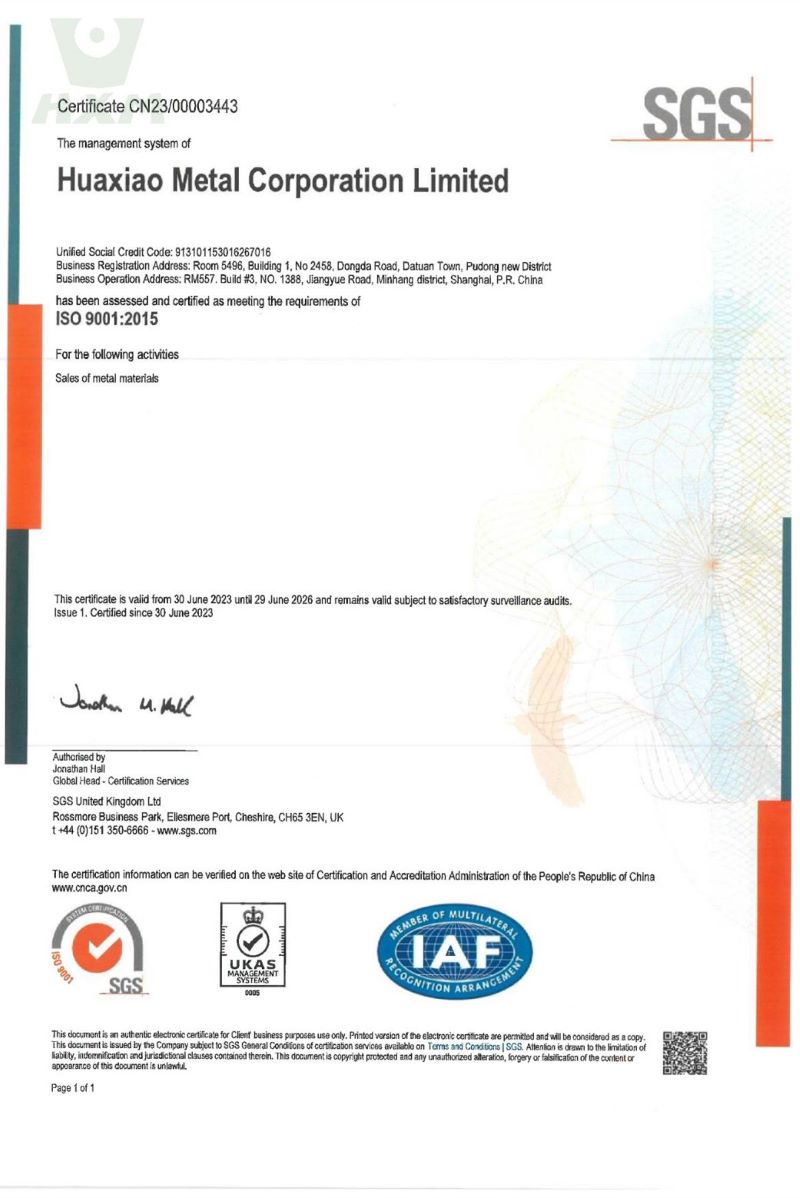
High-Quality Alloys
Our alloys undergo rigorous testing and quality control processes to ensure exceptional performance, durability, and reliability.When you choose us, you can have confidence in the superior quality of our products.
Reliable Supply Chain
As your trusted iron alloy suppliers, we maintain a reliable and efficient supply chain to ensure the timely delivery of your orders. You can rely on us to meet your production deadlines and keep your operations running smoothly.
Customer Satisfaction
At Alloyours, we prioritize customer satisfaction.We are committed to delivering high-quality alloys, customized solutions, and exceptional service to meet your alloy needs. Let us be your trusted iron alloy suppliers in alloy supply.
Building The Future
Latest From the Blog
CONTACT US
Ready to take your projects to new heights with premium nickel alloy solutions? Our expert team is here to provide tailored advice, competitive pricing, and exceptional customer service. Reach out to us today and let’s create success together!